Recytyre
- innekedc
- 29 févr. 2024
- 4 min de lecture
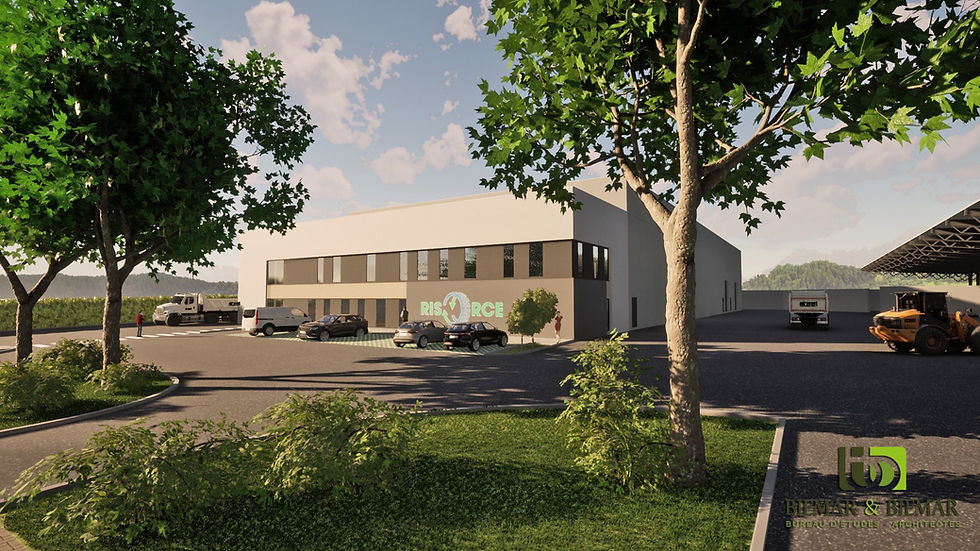
Circularité et un ancrage local Une usine de recyclage ultramoderne et tournée vers l’avenir est en cours de construction dans la province de Liège. L’objectif : traiter les restes de pneus de voiture broyés (“shredded”). La réalisation du projet‘RISORCE’ (Renewable, Innovative Solutions towards Recycling & Circular Economy) est possible grâce au soutien de la Fondation Roi Baudouin, avec l’aval de Recytyre.
« Pour chaque nouveau pneu vendu, une contribution environnementale est facturée au client final, ce qui contribue à réaliser le projet “RISORCE””, explique Chris Lorquet, CEO de Recytyre. “ Chaque année, Recytyre fait un don à la Fondation Roi Baudouin. Ceci à travers le fonds d’investissement GREEN.er, créé en 2017 à l’initiative de Recytyre, pour soutenir des projets innovants liés à l’industrie du caoutchouc. Le fonds GREEN. er, qui se concentre sur la diversification des débouchés des matières premières issues du recyclage des pneus usagés en Belgique, est l’un des actionnaires de RISORCE”. Après quatre années d’intense préparation, le projet RISORCE est en cours de construction dans la Zone de développement “East Belgium Park” à Baelen, dans la province de Liège. La première unité sera construite dès le dernier trimestre 2024 et les suivantes ensuite, de manière à ce que le site soit pleinement opérationnel fin 2025. Un certain nombre de conditions ont été fixées lors de l’élaboration du concept, notamment un ancrage belge/ local à 100 % et 0% de technologie chinoise.

La matière première: les pneus usagés Recytyre, qui gère les flux de pneus usagés en Belgique, traite une moyenne annuelle de 80 000 tonnes de pneus et collecte efficacement tout ce qui est présenté comme des pneus usagés. “C’est même plus que ce qui est vendu neuf” complète Chris Lorquet. Après avoir extrait les matières textiles et métalliques des pneus de voitures et de camionnettes usagés, ceux-ci sont déchiquetés en granulats. Sur les 40 partenaires agréés par Recytyre pour la collecte et le traitement des pneus déportés, seuls deux vont jusqu’à cette étape de traitement. C’est là que RISORCE entre en jeu. Bernard Van de Wouwer, CEO de RISORCE, déclare : “Nous nous approvisionnons à 100 % auprès de partenaires homologués par Recytyre et nous fonctionnerons donc entièrement avec des pneus usagés belges. Nous proposons une solution localement ancrée et robuste, tant sur le plan technologique qu’au niveau environnemental et de l’emploi”. Les broyats de pneus sont introduits dans un grand moule en forme de tonneau, qui fonctionne comme une sorte de four à pyrolyse. Dans un environnement pauvre en oxygène, ils sont chauffés à 450-500°C. Il est ainsi possible de séparer davantage les broyats de pneus. Le caoutchouc s’évapore et est recueilli, puis rapidement refroidi à +/- 20°C. Ce processus de condensation (passa-ge de la forme vapeur à la forme liquide) aboutit à de l’huile de pyrolyse, un produit qui trouve des débouchés dans les raffineries de pétrole. Le caoutchouc utilisé pour la fabrication des pneus est à 50 % d’origine fossile (noir) et à 50 % issu de l’hévéa (vert). Le pétrole vert est mélangé au pétrole noir par les compagnies pétrolières. La même propriété permet d’obtenir l’huile de pyrolyse qui sera produite par RISORCE. “Elle peut être entièrement mélangée et traitée dans les installations existantes”, déclare Bernard Van de Wouwer. “L’Europe impose également de plus en plus l’utilisation de pétrole vert afin d’éliminer progressivement le pétrole fossile”, poursuit Chris Lorquet. “RISORCE contribue donc encore davantage à l’écologisation”.
Optimiser la valorisation
“Une partie des gaz libérés - environ 10 % - est conservée sous forme gazeuse”, poursuit Bernard Van de Wouwer. “Le gaz étant similaire au méthane et au propane, il convient donc parfaitement à l’alimentation de nos brûleurs. C’est là un point crucial dans la poursuite de la circularité, mais il libère aussi un volume de gaz plus important que celui nécessaire pour les brûleurs qui chauffent les broyats de pneus. Il reste suffisamment de gaz pour chauffer nos bâtiments - et fort probablement encore plus pour produire de l’électricité. On peut donc parler d’un processus neutre, voire positif, sur le plan de l’énergie thermique”. Outre l’huile de pyrolyse en tant que produit final commercialisable et les gaz nécessaires au fonctionnement de l’usine de traitement, des résidus subsistent dans le four. “Il s’agit de RCB - Recycled Carbon Black - qui sera vendu aux fabricants de produits en caoutchouc noir. Il s’agit notamment de combinaisons de plongée noires, de bandes transporteuses dans les aéroports et l’industrie… Bernard Van de Wouwer: “Aujourd’hui, avant même que le site RISORCE ne soit achevé, nous pouvons déjà affirmer qu’il y a une demande suffisante pour nos produits finis. Mieux encore, les flux entrants de copeaux de pneus et les flux sortants d’huile de pyrolyse et de noir de carbone récupéré (RCB) sont déjà assurés à 100 %. De plus, l’Europe impose une interdiction d’exportation des déchets de pneus à partir de 2025, ce qui signifie un traitement local obligatoire, et donc une garantie supplémentaire pour nos flux entrants”. À terme, RISORCE prévoit de traiter 18 000 tonnes de flux entrants, soit 1 pneu sur 2 présenté comme un déchet en Belgique. Les promoteurs eux-mêmes s’attendent à ce que RISORCE ne reste pas un phénomène unique en Belgique. La concurrence leur semble également une bonne chose. Un projet similaire devrait probablement voir le jour dans le port d’Anvers.
Une technologie qui a fait ses preuves
La technologie utilisée par RISORCE pour ce processus de traitement a été testée de manière approfondie avant le début de la construction. “Nous avons trouvé ce qu’il nous fallait en Bosnie-Herzégovine, une république fédérale du sud-est de l’Europe”, explique Bernard Van de Wouwer. “Plus important encore : nous avons pu réaliser une configuration pilote à l’échelle 1:1, afin de tout tester en conditions réelles avant de donner le feu vert final à la construction en Belgique. Les pneus belges ont été utilisés pour les essais, de sorte que rien n’a été laissé au hasard. En achetant une technologie éprouvée, nous n’avons pas besoin d’expérimenter nous-mêmes et les risques pour l’entreprise sont réduits au strict minimum”.

Comentários